On-site electrochlorination systems are a sustainable, effective and cost-friendly solution for water disinfection in various industries. Electrochlorination is a process using electricity to convert saltwater into sodium hypochlorite or chlorine gas, which are powerful disinfectants. De Nora, a leading provider of electrochemical technologies, offers different products, including CECHLO™, ClorTec®, and MIOX® systems, which produce sodium hypochlorite in differerent concentration and chlorine gas . In this blog post, we will address common questions about electrochlorination, its benefits, how to choose the right brine system for your application, considering the initial investment, maintenance, lifespan and operating cost. We will also provide an overview of our different electrochlorination products.
Generating sodium hypochlorite and chlorine gas with on-site electrochlorination: How it works and the benefits it provides
Why do treatment operations need to generate sodium hypochlorite?
Most water and wastewater treatment require the disinfection of the potable water before its injection into the distribution system or wastewater effluent. This process is a crucial step in preventing pathogens, viruses, and harmful bacteria from being released into the environment.
Today, chlorination remains one of the most widely utilized disinfection methods for both water and wastewater treatment processes at both municipal and industrial facilities. Additionally, chlorine is one of only a few chemicals that provide a residual that carries from the water treatment plant through the water distribution system and to the end user’s tap.
Chlorine can be utilized in the form of pure gas, as a solid in the form of calcium hypochlorite, or as a liquid in the form of sodium hypochlorite. Making sodium hypochlorite at the facility using an on-site sodium hypochlorite generation (OSHG) system is a cheap, easy and effective way to provide chlorine for disinfection.
What is an electrochlorination system?
Electrochlorination uses electricity to convert saltwater into sodium hypochlorite or chlorine gas. The process generates a chlorine-based solution from either delivered food-grade salt (brine) or seawater . In most cases, brine systems are used if the water is destined for human consumption. Seawater systems can be used to treat process water, cooling water, wastewater and other industrial water, such as fire water, at coastal locations where seawater is plentiful, or in offshore oil and gas operations and on ships and vessels.
How does electrochlorination work?
During electrochlorination, an electric current is passed through saltwater, causing chloride ions from the salt solution to oxidize and form molecular chlorine, as gas or sodium hypochlorite depending on the cell design and the process conditions. This on-site process is available from De Nora in different designs, all offering multiple benefits to end users.
What are the benefits of using on-site electrochlorination for water disinfection in water and wastewater treatment plants?
- 1. Safer: On-site electrochlorination systems produce a sodium hypochlorite solution with a concentration range between 0.4% - 0.8% and at a pH of less than 10; this solution is considered a non-hazardous chemical. As a result, this solution does not present a threat to public safety or require extensive risk-management plans for its handling and use.. Hydrogen produced as by-product during electrolysis is safely contained, rapidly diluted, and carefully vented into the atmosphere. Another safety feature is that on-site electrochlorination eliminates the need for storage and transportation of hazardous chemicals.
- 2. Less expensive: The cost of generating chlorine using an on-site electrochlorination system is typically much less than the cost of purchasing an equivalent amount of chlorine in the form of bulk sodium hypochlorite.
- 3. Reduced formation of chlorine byproducts: Bulk sodium hypochlorite will decompose during storage, causing the formation of chlorine disinfection byproducts such as chlorate. Conversely, sodium hypochlorite produced from an on-site electrochlorination system is typically used for dosing within hours of production, significantly reducing degradation and the formation of chlorine byproducts. Some chlorate can also be produced during electrochlorination processes as byproduct due to low efficiency of the electrochemical reaction, but De Nora scientists and engineers have studied this aspect of the process for over a decade and developed a patent-pending solution able to minimize the formation of chlorate during electrolysis.
- 4. More sustainable: Due to greatly reduced waste, lower health and environmental safety threats of transporting and storing bulk concentrated chlorine, reduced byproduct formation, and minimized CO2 footprint, on-site electrochlorination is the most sustainable practice for water disinfection.
- 5. More reliable: By generating its own sodium hypochlorite and chlorine gas, a plant no longer has to rely on purchasing chemical products from the market, which are more vulnerable to price fluctuations, depletion and delivery delays than water, salt and electricity.
What are the advantages of using a hypochlorite generator for disinfection?
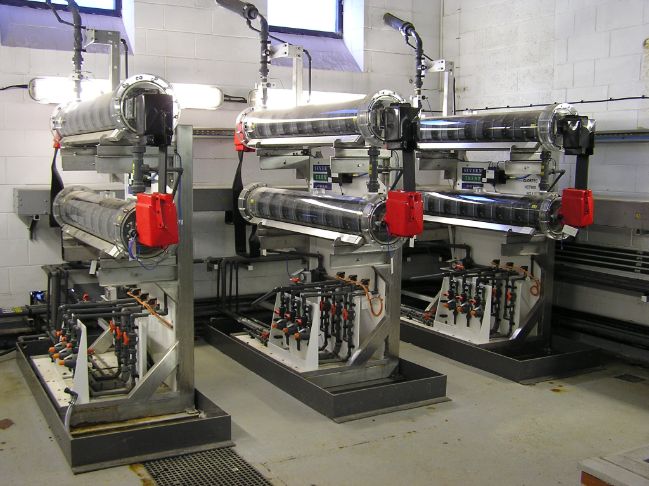
With on-site electrochlorination, a hypochlorite solution can be produced as needed using only water, salt and electricity, ensureing a fresh and reliable supply of disinfectant without the need for bulk chemicals transportation and/or long-term storage. Different systems can produce different concentrations for operations that have more than one disinfection requirement. Also, on-site electrochlorination systems can provide a consistent concentration and reliable supply of sodium hypochlorite solution, ensuring effective disinfection and microbial control.
How do I choose the right electrochlorination system for my application?
De Nora offers three on-site electrochlorination systems using delivered salt, or brine, as an input: CECHLO™, ClorTec and MIOX. The choice of which system to use is based largely on your specific application needs.
CECHLO™-MS systems can produce active chlorine at a rate of 250kg/day to 3000kg/day (551lbs/day to 6614lbs/day) where the chlorine can come in the form of chlorine gas or 12.5% sodium hypochlorite. It can be used for water and wastewater treatment disinfection, bleach manufacturing and wholesale chemical production. Industries that use CECHLO™ systems include municipal potable and wastewater treatment, industrial wastewater treatment, onshore oil and gas operations, power and energy, and water reuse and reclamation. CECHLO™ is the best option for extremely high production capacity requirements (2 tons FAC/day or more) or situations where on-site generated chlorine gas or high concentration sodium hypochlorite would be beneficial.
ClorTec installations can produce chlorine from 6kg/day to 1500 kg/day (13lbs/day to 3307lbs/day) as a 0.8% chlorine concentration hypochlorite solution. It’s the best option for the direct replacement of bulk sodium hypochlorite, especially in the case of moderate production capacity requirements or where access to high quality salt is limited. Common applications include municipal potable water and wastewater treatment and upstream oilfield water treatment.
MIOX technology uses an advanced mixed oxidant solution (MOS) process to generate chlorine-based solutions from 0.45kg/day to 540 kg/day (1lb/day to 1191lbs/day) with a chlorine content of 0.4%. This chlorine-based solution has all the oxidant power of hypochlorite with additional treatment benefits, including biofilm removal and improved microbial inactivation efficacy. With mixed oxidant solution, customers maintain more consistent control over residuals which is often achieved with a lower applied dosage. MIOX technology is the best option for enhanced disinfection. Common applications include municipal potable water treatment when using surface source water or if there are organic disinfection byproduct challenges, or for industrial process water, especially in the case of cooling water treatment.
What equipment do I need for sodium hypochlorite production?
While each application will have its unique needs, the basic components of an on-site electrochlorination system include a water softener, water filter, brine tank, electrolyzer, oxidant tank and injection pump. While not always required, a water heater/chiller unit is another common piece of equipment.
What is the maintenance required for electrochlorination systems?
The maintenance of an electrochlorination system is relatively simple. Regular system monitoring is crucial, as well as following manufacturer maintenance guidelines, which include acid cleaning the electrolytic cell(s), depending on specific site conditions.
To minimize maintenance, we highly recommend starting with high quality salt and water (see the next section, “How long does an electrochlorination system last?” for detail). Assuming this important step is in place, plant operators can expect to remove scales from electrolytic cells using acid washing about once a quarter, on average.
Traditionally, a manual acid washing procedure removes these scales. However, MIOX technology has a proprietary reverse polarity mechanism that can safely clean electrode surfaces. Instead of using an external acid, the direction the current passing through the cell is reversed, so positive becomes negative and negative becomes positive. When this occurs, scales are dissolved from the surface of the electrodes, dramatically reducing the need for external acid washing.
How long does an electrochlorination system last?
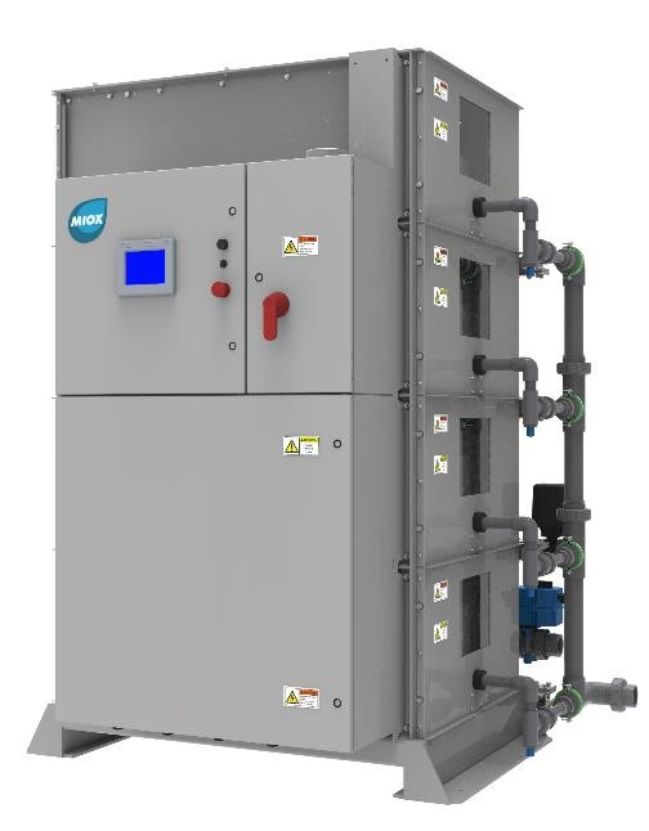
In a well-maintained application, electrochlorination systems can last for as long as 20 years. As the electrolytic cell is half the cost of the system, it’s important to pay special attention to cell maintenance.
During electrolysis, the aqueous environment near the cathode surface exists in a very high pH environment, which drives the precipitation of calcium carbonate and magnesium hydroxide, two of the most common scales that can form in electrochlorination cells. This can be minimized by starting with high quality water. It is very important that the water be softened to maintain the feed water hardness within the recommended range. If hard water is used to provide either the water or brine solutions for an electrolytic cell, scale will rapidly form on the surfaces of the cathodes, causing the electrolytic cell to fail. Similarly, the temperature of the water entering the electrolytic cell should be maintained within a range of 10 ̊C to 27 ̊C (50 ̊ to 80 ̊F) to avoid damaging the electrolytic cell. If an electrochlorination system is installed where water feeding the system will be outside of that temperature range, a heater/chiller unit is typically added to the overall system.
High quality salt also is critically important to preventing scale development. Sodium chloride is the only chemical added to the electrochlorination water stream and is required for producing the chlorine and hypochlorite. As is the case with feed water, it is vital to use high purity salt to ensure reliable operation. Some contaminants in salt, such as the calcium and magnesium found in brackish waters and sea salt, can damage the electrolytic cell. Another concern is that some salts contain other chemical species that are subject to oxidation, the most common being bromide (Br-). In any electrochemical cell that produces chlorine, bromide will be oxidized to form bromates (BrO3-), which are regulated by the EPA to have a Maximum Contaminant Limit (MCL) of 0.01 mg/L (8lbs/gallon) in drinking water. Food quality salt is the most common form of salt recommended for electrochlorination systems.
When scales do form, cleaning them regularly (once a quarter, on average) is important to maximize the life of the cell. Traditionally, a manual acid washing procedure removes these scales. However, MIOX systems have a proprietary reverse polarity mechanism that can safely clean electrode surfaces. Instead of using an external acid, the direction the current passing through the cell is reversed, so positive becomes negative and negative becomes positive. When this occurs, scales are dissolved from the surface of the electrodes, dramatically reducing the need for external acid washing.
Can on-site electrochlorination be used for other applications besides water disinfection?
Electrochlorination systems are used for water disinfection in multiple applications in drinking water, wastewater and industrial water settings. Additionally, electrochlorination can be used in other applications such as chemical oxidation for inorganic components (such as iron), removing hydrogen sulfide in industrial processing and in some instances, ammonia removal.
It should be noted that a single on-site generator can be used for multiple applications at a site. This allows operators to take advantage of economies of scale provided by on-site electrochlorination systems.
What is the cost of an on-site electrochlorination system, and how does it compare to other disinfection technologies?
The cost of an on-site electrochlorination system can range from $12,000 to more than $1 million, based on the scope and size required. These capital costs can be recouped through operational savings, especially when considering the cost of purchasing bulk sodium hypochlorite. The cost of generating sodium hypochlorite on-site is typically in the range of $0.60 to $0.70 per pound, as compared to as much as $3.00 per pound to buy bulk hypochlorite. Depending on how much chlorine a plant needs and what it typically pays for bulk sodium hypochlorite, plant operators can calculate how much savings the plant would realize from generating its own.
What are some of the primary safety concerns that need to be addressed before generating sodium hypochlorite on-site?
OSHG is by far the safest method of disinfecting with chlorine since the raw materials are salt, water, and electricity. Although one potentially dangerous byproduct, hydrogen, is produced during the electrolysis of brine, it is safely contained, rapidly diluted, and carefully vented into the atmosphere.
Before you begin to generate sodium hypochlorite on-site, it is essential to have built-in safeguards, including a hydrogen detector to shut the entire system down if the concentration of hydrogen exceeds specific parameters. It is also vital to select a vendor that offers a quality system designed with safety in mind.
What customers and industry needs inspired the development of the ClorTec® on-site hypochlorite generation system ?
On-site hypochlorite generation itself originally started in the swimming pool industry as a safer alternative to chlorine gas and a cheaper alternative to bulk sodium hypochlorite. It quickly spread into the municipal water and wastewater disinfection industry for the same reasons.
As more and more on-site hypochlorite generation systems were installed, a need for simpler, safer, reliable, efficient and less-expensive equipment was recognized. The De Nora model utilizes the same basic system as previous models while being simpler to operate, safer to maintain, and able to deliver many unique operating advantages.
Let De Nora help you design an electrochlorination system that fits your needs
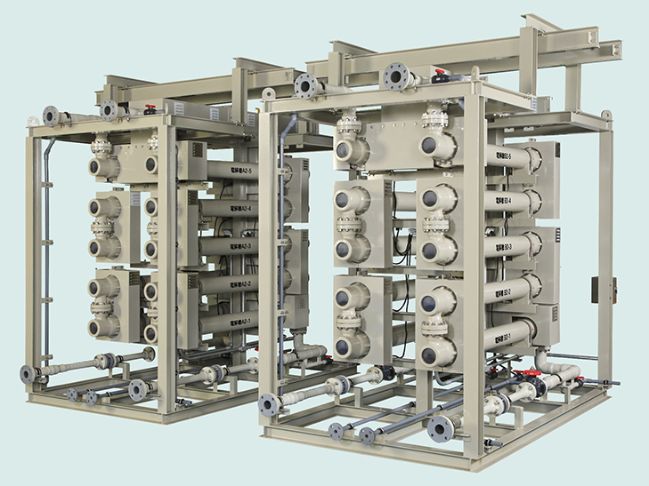
On-site electrochlorination systems are a reliable and sustainable solution for water disinfection in various industries. De Nora offers a range of electrochlorination products, including CECHLO™, ClorTec, and MIOX systems, that produce sodium hypochlorite and chlorine gas in varying capacities. This blog post aims to provide readers with a better understanding of electrochlorination, its benefits, and how to match the right system with the intended application.
De Nora is a market in electrochemical technologies, and we welcome any questions you have about the technology or our products.