For operations that disinfect water and wastewater and are located on the coast or an offshore platform, seawater electrochlorination (SWEC) systems are a reliable and efficient means of on-site generation of sodium hypochlorite to prevent biofouling, using just seawater and electricity.
Seawater electrochlorination assures reliable supply of sodium hypochlorite to prevent marine biofouling in offshore and onshore applications
What is biofouling and why is it a problem?

While using seawater for various onshore and offshore applications and processes taps a reliable and plentiful supply of intake water, seawater contains a large amount of marine life. These organisms will naturally attach and grow throughout a system, eventually leading to system blockage, a reduced flow, a drop in performance and eventual system failure. This process is known as biofouling and can be prevented with a consistent application of a disinfectant, like sodium hypochlorite. With a seawater electrochlorination system, onshore and offshore facilities can confidently use seawater without the concern of biofouling – for both their processes that use seawater and for the electrochlorination system itself.
What is a seawater electrochlorination system?
Electrochlorination uses electricity to convert saltwater into sodium hypochlorite. The process generates a chlorine-based solution from seawater and can be used to treat process water, cooling water, wastewater and other industrial water at coastal locations where seawater is plentiful, or in offshore platform operations. Common applications for seawater electrochlorination systems include oil and gas, petrochemical, energy generation (among others, wind, nuclear and thermal ), data centers, desalination plants and liquified natural gas terminals.
How does electrochlorination work?
During electrochlorination, an electric current is passed through saltwater in an electrolytic cell, causing the formation of sodium hypochlorite. Through on-site seawater electrochlorination technology and proprietary, industry-leading DSA® electrodes from De Nora, SEACLOR® and SANILEC® systems can produce sodium hypochlorite at a concentration of 0.1% to 0.2%, offering multiple benefits to end users.
What are the benefits of using seawater electrochlorination for biofouling control?
- 1. Better performance against biofouling: A De Nora seawater electrochlorination system injects a steady dose of sodium hypochlorite into all areas where marine biofouling occurs, preventing buildup from starting.
- 2. Safer: Because sodium hypochlorite is typically used immediately in onshore and offshore operations, on-site seawater electrochlorination systems eliminate the need for storage and transportation of hazardous chemicals.
- 3. Less expensive: The cost of generating a pound of chlorine using an on-site electrochlorination system is typically much less than the cost of purchasing and transporting a pound of chlorine.
- 4. More sustainable: Due to greatly reduced waste, lower health threats and less environmental impact, on-site electrochlorination is a more sustainable practice.
- 5. Less vulnerable supply: By generating its own sodium hypochlorite using just electricity and seawater, a plant doesn’t have to buy disinfectant from the market, which is subject to price fluctuations and delivery delays.
What is the difference between onshore and offshore seawater electrochlorination systems?
The main difference between onshore and offshore seawater electrochlorination systems is the constraint on space. For onshore systems, space isn’t as much of an issue, so operators typically use a De Nora SEACLOR system, which consolidates electrochlorination into one or two large cells.
For offshore platforms, space constraints affect almost every decision. De Nora SANILEC systems offer the same exceptional performance but with two key differences. First, SANILEC is a modular system and consists of multiple smaller cells that can be custom configured to fit small spaces. Second, SANILEC is equipped with a proprietary reverse polarity mechanism that can safely clean electrode surfaces. Instead of using an external acid, the direction of the current passing through the cell is reversed, so positive becomes negative and negative becomes positive. When this occurs, scales are dissolved from the surface of the electrodes, dramatically reducing the need for external acid washing. This feature reduces the need to store acid as well as the labor required for acid washing.
How does SEACLOR work?
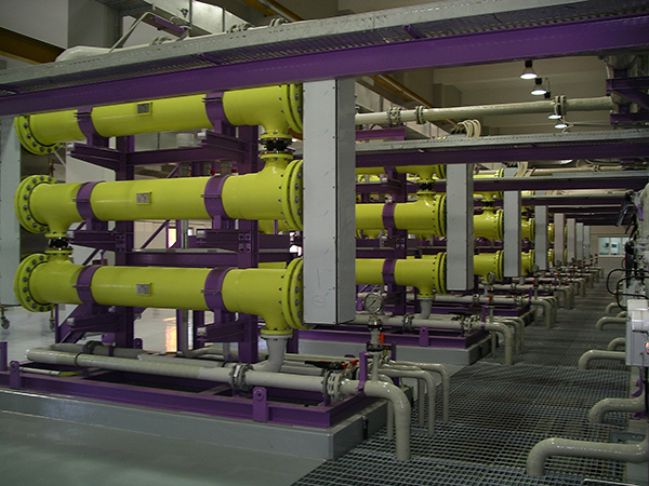
SEACLOR is based on the electrolysis of seawater as it flows through an unseparated electrolytic cell. Pressurized seawater is delivered to the SEACLOR system where it is filtered to remove suspended solids larger than 0.5mm before entering the cells. The seawater is forced through a flow control assembly that ensures optimum control of speed and volume of the seawater. It enters the electrolyzer cells, where an electric current is applied to electrodes, and exits as sodium hypochlorite solution. This two-phase solution is piped to a tank where hydrogen gas is vented to the atmosphere with the help of a blower. Finally, the sodium hypochlorite solution is injected as required either continuously and/or with shock-dose rates.
Standard SEACLOR systems range in capacity starting at 480 kg/day to 21,600 kg/day (1058 lb/day to 47,620 lb/day) per train with higher capacities achieved by adding trains. SEACLOR seawater electrochlorination systems are designed and assembled for continuous and unattended operation requiring minimal remote monitoring.
How does SANILEC work?
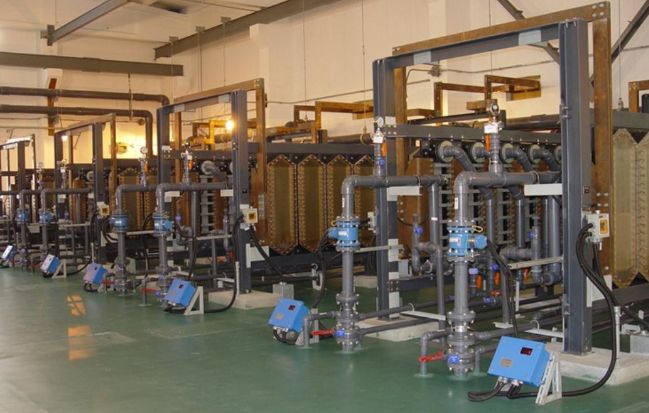
Offshore seawater electrochlorination involves the utilization of an advanced electrochemical cell to convert seawater into sodium hypochlorite, a highly effective disinfectant and oxidizing agent used in water treatment applications. De Nora SANILEC systems incorporate electrolysis technology to generate sodium hypochlorite on-site, catering to the unique requirements of offshore operations.
In a SANILEC system, the seawater passes through a flow control assembly and then enters the proprietary electrolyzer cells. As it flows through the unseparated electrolytic cell, the seawater undergoes electrolysis, resulting in the conversion of chloride ions into sodium hypochlorite. The electrolyzed seawater exits the cell as a two-phase solution, which is then piped to a tank where hydrogen gas is removed. Finally, the sodium hypochlorite solution is injected at the required continuous and/or shock-dose rates, providing effective disinfection for the offshore environment.
SANILEC units come as a modular system that allows it to fit into limited and constrained spaces. Additionally, it’s a self-cleaning system with a proprietary mechanism that safely cleans electrode surfaces by reversing the polarity of the current and dissolving scales from the electrodes.
What is the maintenance required for seawater electrochlorination systems?
The maintenance of a seawater electrochlorination system is relatively simple. Regular system monitoring is crucial, as well as following manufacturer maintenance guidelines. Maintenance is centered on keeping the electrolytic cells clean, and how often they will need cleaning will depend in part on specific site conditions. For example, if a seawater electrochlorination system is located near other industrial operations, the seawater may have a higher content of iron or manganese. Also, salinity in seawater varies from location to location and will have a varying impact on how often electrolytic cells need cleaning.
For SEACLOR, maintenance includes cleaning the electrolytic cell(s) with an acid wash, which takes just a few minutes. Generally speaking, the cells are cleaned about once every month.
For SANILEC, the system includes a proprietary reverse polarity mechanism that can safely clean electrode surfaces. Instead of using an external acid, the direction of the current passing through the cell is reversed, so positive becomes negative and negative becomes positive. When this occurs, scales are dissolved from the surface of the electrodes, dramatically reducing the need for external acid washing.
How long does a seawater electrochlorination system last?
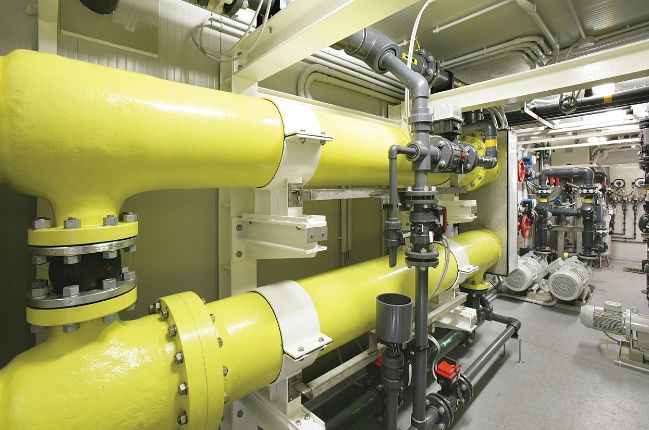
A seawater electrochlorination system can last as long as 30 years or as short as one – it all depends on how well it’s maintained. As the electrolytic cell is a significant portion of the system cost, it’s important to pay special attention to cell maintenance.
In the high pH environment of electrochlorination, electrolysis can result in calcium and magnesium scale forming on the cell. This can be minimized by checking the seawater quality. It is very important that the levels of some pollutants are under a certain threshold. As an example, iron (Fe) should be below 1 ppm and manganese (Mn) below 50 ppb. If those levels are not controlled, the polluted seawater can poison the electrodes, greatly reducing their operating lifecycle.
Similarly, special attention should be given to the temperature of the seawater entering the electrolytic cell. Depending on the operating temperature, De Nora can specify the optimal electrode during the design phase, greatly improving efficiency once in operation.
What does a seawater electrochlorination system cost, and how does it compare to other disinfection technologies?
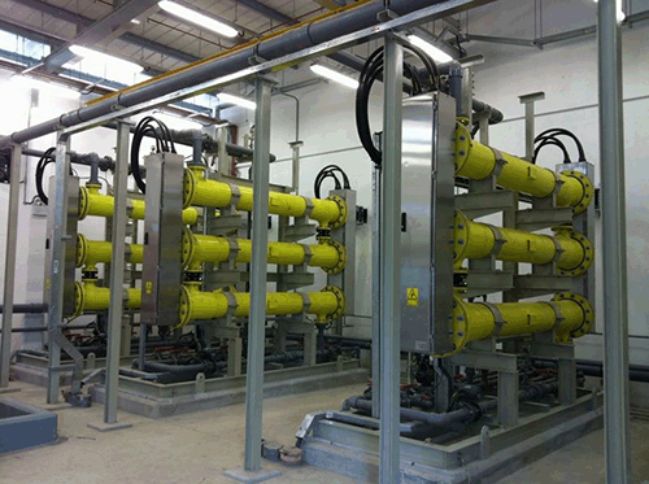
The cost of a seawater electrochlorination system typically starts at $100,000, based on the scope and size required. These capital costs can be recouped through operational savings, especially when considering the cost of purchasing bulk sodium hypochlorite or other chemicals. The cost of generating sodium hypochlorite from seawater electrochlorination varies greatly depending on site, but will be always based on the cost of energy since this is the only input required (aside from seawater). As a rule of thumb, the system consumes about 4 to 4.5 kWh per kg of hypochlorite produced, excluding any accessories (like booster pumps or dosing pumps). Depending on how much disinfectant a plant needs and what it typically pays for bulk, plant operators can calculate how much savings the plant would realize from generating its own.
How can working with De Nora make a difference?
As the world leader for seawater electrochlorination technology, De Nora has more than 1,200 installations in 60 countries, producing over 1.3 million kilograms per day of sodium hypochlorite from seawater, equaling 60-70% of the world capacity.
Due to our 100-year legacy in electrochemistry, companies find great value in working with De Nora. Our robust and proven electrochemical solutions are under a continual development process for ever-improving performance regarding simplicity, safety, sustainability, efficiency and output. With our knowledge of electrochemical processes and our proprietary DSA electrodes, we optimize operation in a broad range of applications. Our expertise makes all the difference between an operation that surpasses goals and one that does not.